
Behind every smooth parking, there is an inconspicuous but vital component-the brake shoe. Although it is hidden in the complex mechanism, it is the key to ensure the braking performance of the vehicle.
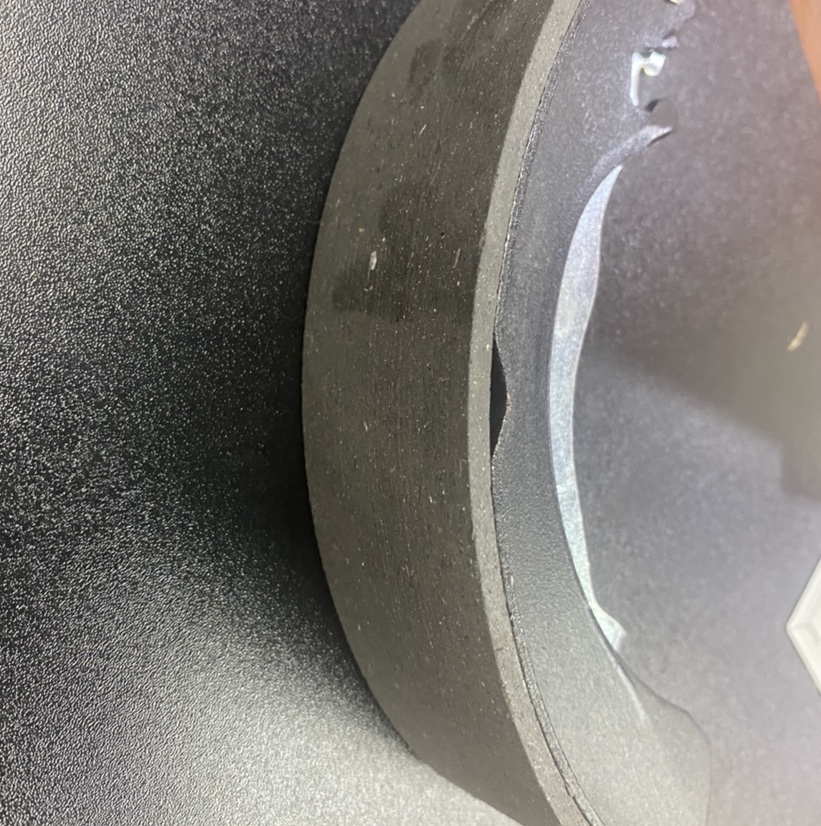
Revealing the secret of the brake shoe-the hero behind the car brake system
The brake shoe is an important part of the traditional drum brake system, which mainly realizes the function of deceleration and stopping through friction. When the driver steps on the brake pedal, the hydraulic pressure pushes the piston to press the brake shoe against the inner wall of the rotating brake drum, thereby generating enough resistance to gradually stop the wheels. Compared with the disc brake system widely used in recent years, drum brakes have stronger heat resistance and cost advantages, and are particularly common in commercial vehicles. However, disc brakes are more suitable for high-performance passenger cars due to faster heat dissipation and sensitive response.
Shop Guide: Find the Best Brake Shoes for Your Car
Choosing the right brake shoe should not only consider the suitability, but also pay attention to the material quality and manufacturing process. High-quality brake shoes are usually made of high-carbon steel. This material has good wear resistance and stability, which can effectively extend the service life. In addition, it is also necessary to carefully check whether the specifications of the product are exactly the same as your model, such as thickness, width and fixing hole position and other information must be accurate. If you are not sure about the specific model, you can obtain accurate data by consulting a professional technician or consulting the official service manual.
Periodic inspection cannot be ignored-evaluation standard for brake shoe life
Over time, frequent use will cause the brake shoe surface to wear and thin, which directly affects the braking efficiency. Generally speaking, if the remaining thickness of the brake shoe is found to be lower than the minimum value specified by the manufacturer, it should be replaced in time to avoid potential safety hazards. In addition to observing the appearance, you can also use auditory signals to judge the signs of failure. For example, the harsh metal scratching sound during driving often means that the brake shoes have been excessively worn and need to be repaired immediately.
DIY small classroom: install your own new brake shoes
For those who love to solve vehicle problems by themselves, replacing brake shoes is not an out-of-reach task. First of all, make sure that the preparation work is fully in place, prepare special tools and suit such as wrench set, socket screwdriver, pliers, etc., and strictly follow the instructions in the instructions to implement the operation process. Loosen the wheel nut first, then remove the relevant connecting rod arm mechanism, finally remove the old parts and replace them with brand-new substitutes to complete the whole operation process. Of course, don't forget to recalibrate and adjust the clearance to ensure normal use.
Extending the lifeline-a scientific and reasonable daily maintenance method
In order to maximize the effect of the brake shoe and postpone its scrap date, please be sure to develop good driving habits. Avoid slamming on the emergency brake and plan the deceleration action as far as possible in advance, which can not only reduce the impact load but also save fuel consumption. In addition, attention should also be paid to maintaining a proper tire pressure level because underinflated tires are easy to slip, thus increasing the burden of braking torque and aggravating the fatigue damage degree of each component. In short, only careful care can bring long-term company and enjoy every moment of peace of mind during the journey.
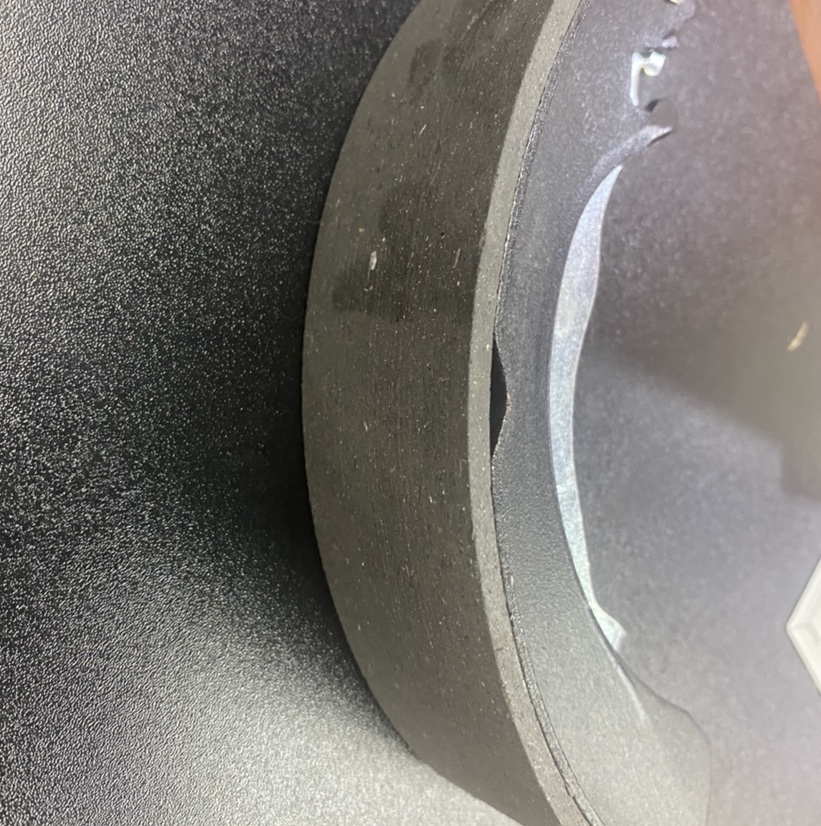